What Are The Specifications Of PVDF Material ?
- websitepetron2016
- Feb 9, 2024
- 4 min read
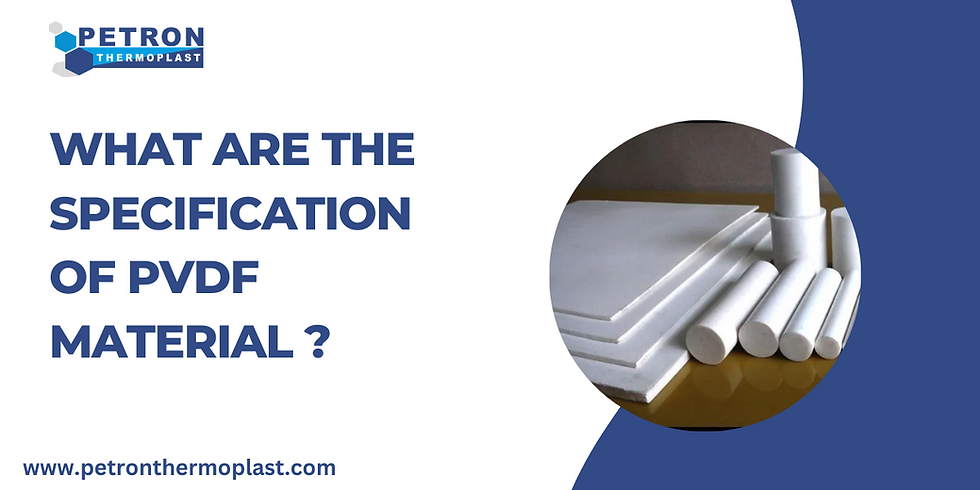
In the world of advanced materials, PVDF material specification stands as a testament to the ingenuity of modern engineering. PVDF, or Polyvinylidene Fluoride, is a thermoplastic fluoropolymer known for its remarkable properties and versatile applications. Let's delve into the intricate details of PVDF Material Specification, exploring its composition, characteristics, and the myriad ways it contributes to various industries.
What is PVDF?
PVDF is a semi-crystalline polymer derived from the polymerization of vinylidene difluoride. This process results in a high molecular weight polymer possessing exceptional chemical resistance, mechanical strength, and thermal stability. One of the distinctive features of PVDF is its fluorine content, which imparts unique properties to the material.
Composition of PVDF:
PVDF primarily consists of carbon, fluorine, and hydrogen atoms arranged in a repeating unit structure. The molecular formula of PVDF is (C2H2F2)n, where 'n' represents the number of repeating units in the polymer chain. This molecular arrangement contributes to the material's robustness and resilience.
Properties of PVDF Material :
1. Chemical Resistance:
PVDF material highlights its exceptional resistance to a wide range of chemicals, including acids, bases, solvents, and oils. This property makes PVDF an ideal choice for applications where exposure to corrosive substances is common, such as chemical processing, pharmaceuticals, and semiconductor manufacturing.
2. Mechanical Strength:
PVDF exhibits impressive mechanical strength and toughness, allowing it to withstand mechanical stress and deformation without compromising its structural integrity. This characteristic makes PVDF suitable for demanding engineering applications, including piping systems, structural components, and aerospace components.
3. Thermal Stability:
PVDF material underscores its excellent thermal stability, enabling it to maintain its properties over a wide temperature range. PVDF can withstand both high and low temperatures without experiencing significant degradation, making it suitable for applications in extreme environments, such as aerospace, automotive, and electrical insulation.
4. Electrical Properties:
PVDF possesses desirable electrical properties, including high dielectric strength, low dielectric constant, and excellent insulating properties. These characteristics make PVDF an ideal material for electrical and electronic applications, such as cables, capacitors, sensors, and piezoelectric devices.
5. Weather Resistance:
PVDF demonstrates outstanding weather resistance, retaining its appearance and properties even after prolonged exposure to UV radiation, moisture, and atmospheric pollutants. This property makes PVDF suitable for outdoor applications, such as architectural coatings, signage, and protective films.
6. Flame Retardancy:
PVDF exhibits inherent flame retardant properties, making it resistant to ignition and combustion. This attribute enhances the safety of PVDF-based products in various applications, including building materials, transportation, and electronics.
7. Biocompatibility:
PVDF is biocompatible, meaning it is well-tolerated by living tissues and exhibits minimal adverse reactions when in contact with biological systems. This property makes PVDF suitable for medical and healthcare applications, including implants, drug delivery systems, and medical devices.
Applications of PVDF Material :
PVDF finds widespread use across various industries, thanks to its exceptional properties and versatility. Some prominent applications of PVDF include:
Chemical Processing: PVDF piping systems, valves, and fittings for handling corrosive chemicals.
Aerospace: Structural components, fuel lines, and insulation materials for aircraft and spacecraft.
Electronics: Cables, connectors, capacitors, and printed circuit boards.
Construction: Architectural coatings, roofing membranes, and protective films.
Medical: Implants, catheters, surgical instruments, and drug delivery systems.
Energy: Photovoltaic films, membranes for fuel cells, and coatings for solar panels.
Automotive: Fuel systems, hoses, gaskets, and interior trim components.
Advantages of PVDF Material
1. Versatility:
PVDF offers a wide range of properties and can be tailored to meet specific application requirements. Its versatility allows engineers and designers to explore innovative solutions across various industries.
2. Durability:
PVDF's inherent resistance to chemicals, UV radiation, and mechanical stress ensures long-term durability and reliability in demanding environments. This durability translates to cost savings and reduced maintenance efforts over the product's lifespan.
3. Environmental Compatibility:
PVDF is an environmentally friendly material, as it is recyclable and does not release harmful substances during its production or use. Its longevity and resistance to weathering contribute to sustainability efforts in various industries.
4. Cost-Effectiveness:
Despite being a high-performance material, PVDF offers cost-effective solutions due to its long lifespan, minimal maintenance requirements, and reduced downtime in industrial applications. Its ability to replace traditional materials in certain applications further enhances cost efficiency.
5. Ease of Processing:
PVDF's versatility extends to its processing capabilities, as it can be easily moulded, extruded, and fabricated into complex shapes using conventional manufacturing techniques such as injection moulding, compression moulding, and extrusion. This ease of processing enhances design flexibility and enables the production of intricate components with precision.
6. Adhesion Properties:
PVDF exhibits excellent adhesion properties, allowing it to bond effectively with a wide range of substrates, including metals, plastics, and composites. This attribute makes PVDF suitable for coating applications where strong adhesion and durability are essential, such as in architectural coatings, automotive paints, and protective films.
7. Regulatory Compliance:
PVDF complies with various regulatory standards and certifications, ensuring its suitability for use in critical applications where safety and reliability are paramount. Whether it's meeting FDA regulations for food contact materials, UL standards for electrical insulation, or ASTM specifications for construction materials, PVDF offers peace of mind to manufacturers and end-users alike.
Future Trends and Innovations:
As technology advances and new challenges emerge, the field of PVDF materials continues to evolve, driven by ongoing research and development efforts. Some emerging trends and innovations in PVDF Material Specification include:
Enhanced Performance Additives: Researchers are exploring the incorporation of nanoparticles, fillers, and additives to further enhance PVDF's properties, such as conductivity, thermal stability, and mechanical strength, opening up new possibilities for advanced applications in electronics, energy storage, and aerospace.
Functionalization: Functionalizing PVDF with tailored chemical groups and surface modifications enables the development of specialised materials with enhanced properties, such as self-cleaning surfaces, antimicrobial coatings, and stimuli-responsive membranes, catering to specific industry needs and emerging applications.
Sustainable Solutions: With growing emphasis on sustainability and environmental stewardship, efforts are underway to develop eco-friendly alternatives to traditional PVDF materials, such as bio-based polymers, recycled PVDF blends, and biodegradable formulations, aligning with the global push towards circular economy principles and reduced carbon footprint.
Conclusion:
In conclusion, PVDF Material encompasses a myriad of properties, applications, and advantages that position it as a premier choice in the realm of advanced materials. From its exceptional chemical resistance to its versatile applications across industries, PVDF continues to push the boundaries of innovation and engineering excellence. As industries evolve and demand for high-performance materials grows, PVDF stands ready to meet the challenges of tomorrow with its unparalleled properties and capabilities.
Kommentare